At a glance:
- With the easing of commodity prices, constraints on supply chains and pressures on productivity, increasing mining organisations are looking for ways to reduce operational costs.
- With improved visibility of their inventory, inventory managers can deliver mining organisations with some quick wins that can directly impact operational costs and free up capital.
- Reviewing and adjusting approaches to the holding and restocking of slow moving and long term inventory items can have significant impact.
In this article we share some insights on how mining organisations can reduce operational costs through better visibility and management of their slow moving or long term inventory items and draw on their data to ensure the right stock levels are maintained.
An easing of commodity prices means mining companies across the globe are looking for ways to reduce operational costs while maintaining production targets, constraints on supply chains and ESG regulatory pressures.
One simple way to deliver quick wins is through maintaining a well-optimised inventory of spare parts and operational materials. Keeping an orderly inventory means the required parts are available while removing working capital from inventory to fund other high priority projects. Over the last few months we have been working with customers on initiatives to use their available data to make informed decisions about inventory investment, lets discuss some of these initiatives now.
1. Managing slow moving items
Managing slow moving items is perhaps one of the most challenging of all inventory tasks. Slow moving items are often characterised by long lead times and high unit prices with usage often aligned to reliability of install base. Investment in slow moving inventory often occurs when assets are commissioned, usage is infrequent meaning opportunities to reduce surplus is few and far between.
We are seeing from customers that the best way to effectively manage this inventory is to undertake a detailed review at the time of demand before replenishment is triggered. It is at this point that significant value can be realised by understanding whether a replacement is actually required, and when the best time to purchase the replacement. Setting up a work queue or task list to identify slow moving materials as soon as a stock movement is recorded is a simple way to add value through robust inventory management.
2. Assessing long term items
Following on with the slow moving theme, it’s not just about the items that are moving but what about those that haven’t moved for a long time? Firstly, what is a long time? To your business it may be 12 months but to a lot of mining companies it may be 5 years or more.
There are a few questions managers of mining inventory should investigate:
- Are we preserving those stock inventory items and materials correctly?
- Are we still using the assets these items maintain?
- What value are we holding the items at?
- How has that the item value changed over the last year?
Inevitably senior managers will at some point will ask about inventory value changes over time and inventory managers will need to be armed with insights as slow and long moving inventory can contribute significantly to the bottom line. Depending on accounting methods used at your organisation, the carrying value may have increased significantly and therefore keeping track of the changes are important to allow tracking and management of inventory values.
3. Consolidate holding of common spares
For those organisations with multiple storage locations across sites it makes sense to consolidate holding of common spares wherever possible using an inventory sharing solution. There are several ways to achieve a robust sharing solution but there are a number of considerations that need to be made before going down this path such as ownership and access priority, and then the standard optimisation inputs such as lead times, usage, price and criticality to name a few.
The optimisation of the reorder levels also needs to take into account where the sharing location is relative to the suppliers and the end users. Inventory sharing can be a great way to make significant inventory savings if the business conditions are right for you.
These quick and relatively easier actions can make a significant difference to your inventory and operational costs, however clear visibility of your data is essential in being able to identify these savings and adjust accordingly.
Getting clearer and more accurate insights about your inventory from your data can be achieved by integrating your ERP with a purpose-built inventory optimisation solution such as IBM's MRO Inventory Optimization (MRO IO). MRO IO has many benefits, but one significant one is the ability to set up work queues (prioritised lists of work) to identify those materials or items in your inventory that have recorded a movement and should be reviewed for reordering approaches and potential savings.
See COSOL demonstrate IBM's MRO Inventory Optimization solution at MINExpo 2024
See live demonstrations daily on how to optimize your MRO inventory to reduce unplanned downtime and costs. Learn how to get a clearer, more accurate view of your MRO inventory and how with the right strategy and tools, you can reduce unplanned downtime due to parts by 50%, reduce inventory costs by 40% and contribute to your commitment to carbon reduction. Features IBM's MRO Inventory Optimization platform which easily integrates with leading ERP's and EAMs.
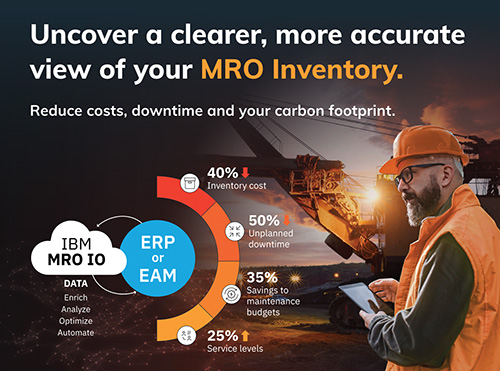
About IBM's MRO Inventory Optimization solution
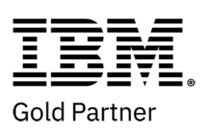