At a glance
-
Predictive AI helps identify asset issues early—before they escalate.
-
Real-time monitoring enables fast, focused responses to subtle changes.
-
Fewer breakdowns mean less disruption, lower costs, and safer operations.
-
Resilient systems empower teams to plan ahead and act with confidence.
Every asset manager knows the stress of something breaking down without warning. It throws off schedules, creates safety risks, and often ends up costing far more than expected.
No one wants to work in reactive mode, constantly chasing problems. But the reality is, many organisations still rely on systems that don’t surface risks until it’s too late.
That’s beginning to change. With better data and smarter tools, it’s now possible to identify issues early and act before they escalate.
AI and predictive analytics are making this shift more accessible. Not by replacing teams, but by helping them plan, prevent and stay one step ahead.
The cost of waiting too long
Unplanned downtime is one of the most disruptive and expensive challenges in asset management. It leads to urgent decisions, increased costs and lost time across the board.
The challenge is that many failures feel sudden. A small issue goes unnoticed, and by the time it becomes visible, it’s already impacting performance or reliability.
The key is early insight. When teams can detect risk before it turns into failure, they can plan more effectively and protect service continuity.
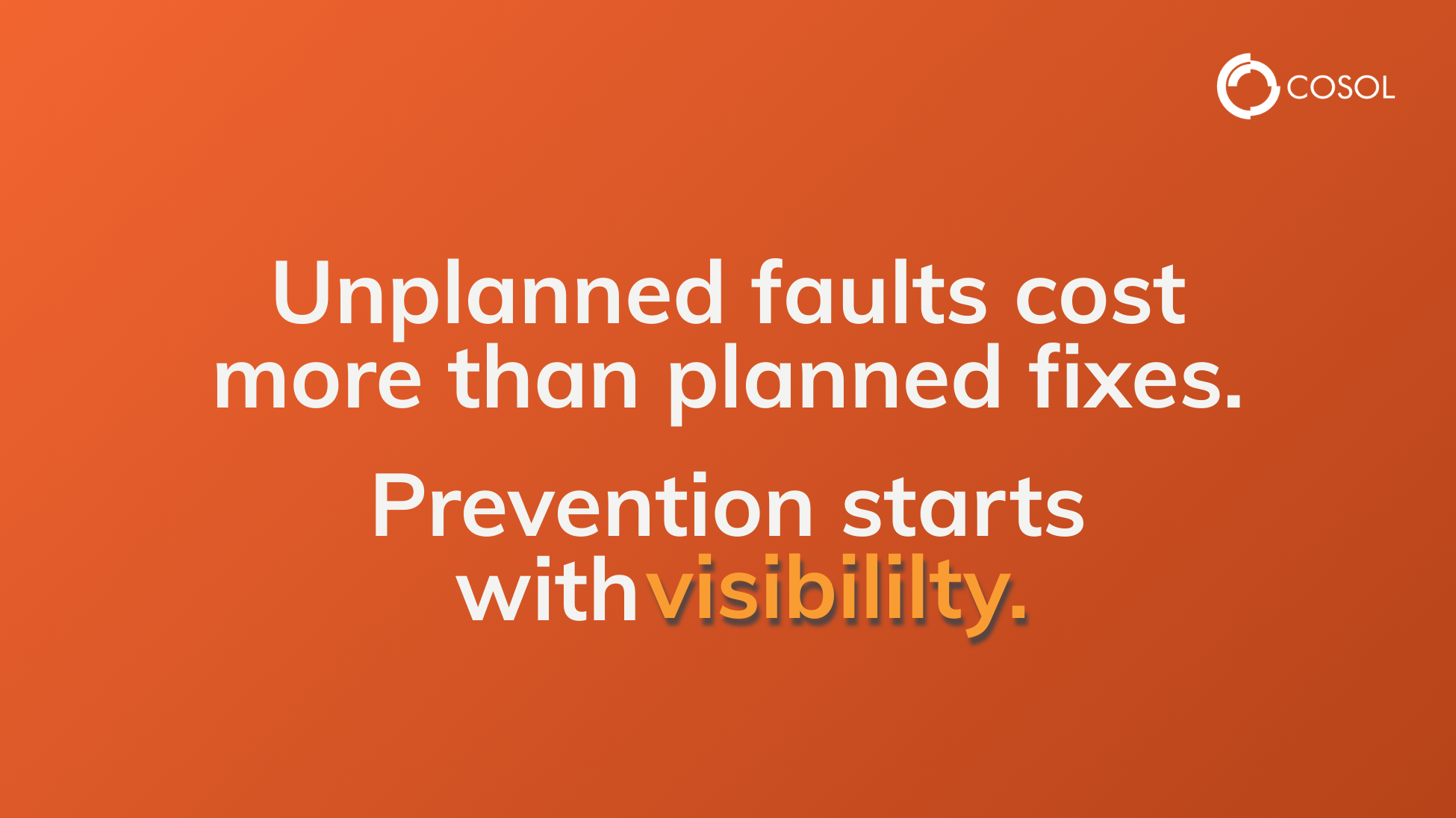
How AI changes the equation
Predictive maintenance uses data from inspections, sensors and operating conditions to estimate when assets might begin to degrade.
AI models analyse patterns and highlight small shifts that may otherwise go unnoticed, such as changes in vibration, temperature or flow that signal early wear or risk.
Rather than waiting for something to break, AI helps teams see when equipment is trending outside its normal range. That creates time to act.
It’s not about doing more. It’s about doing what matters, when it matters.
Some of the benefits include:
-
Fewer unexpected breakdowns
-
Less overtime and emergency call-outs
-
Reduced service disruptions
-
More consistent asset performance
Staying alert in real-time
When AI systems are connected to real-time monitoring tools, alerts can be triggered as soon as something starts to change.
A pressure dip. A vibration spike. A shift in load. These subtle signals become useful when they’re captured in the moment and passed to the right people.
In a treatment plant, this might mean detecting a pump issue before water pressure is affected. On a rail line, it might be catching a signal fault before it leads to peak-hour delays.
Real-time visibility helps maintenance teams stay focused on what matters and gives operators the breathing room to plan a response instead of racing to fix a problem after it breaks.
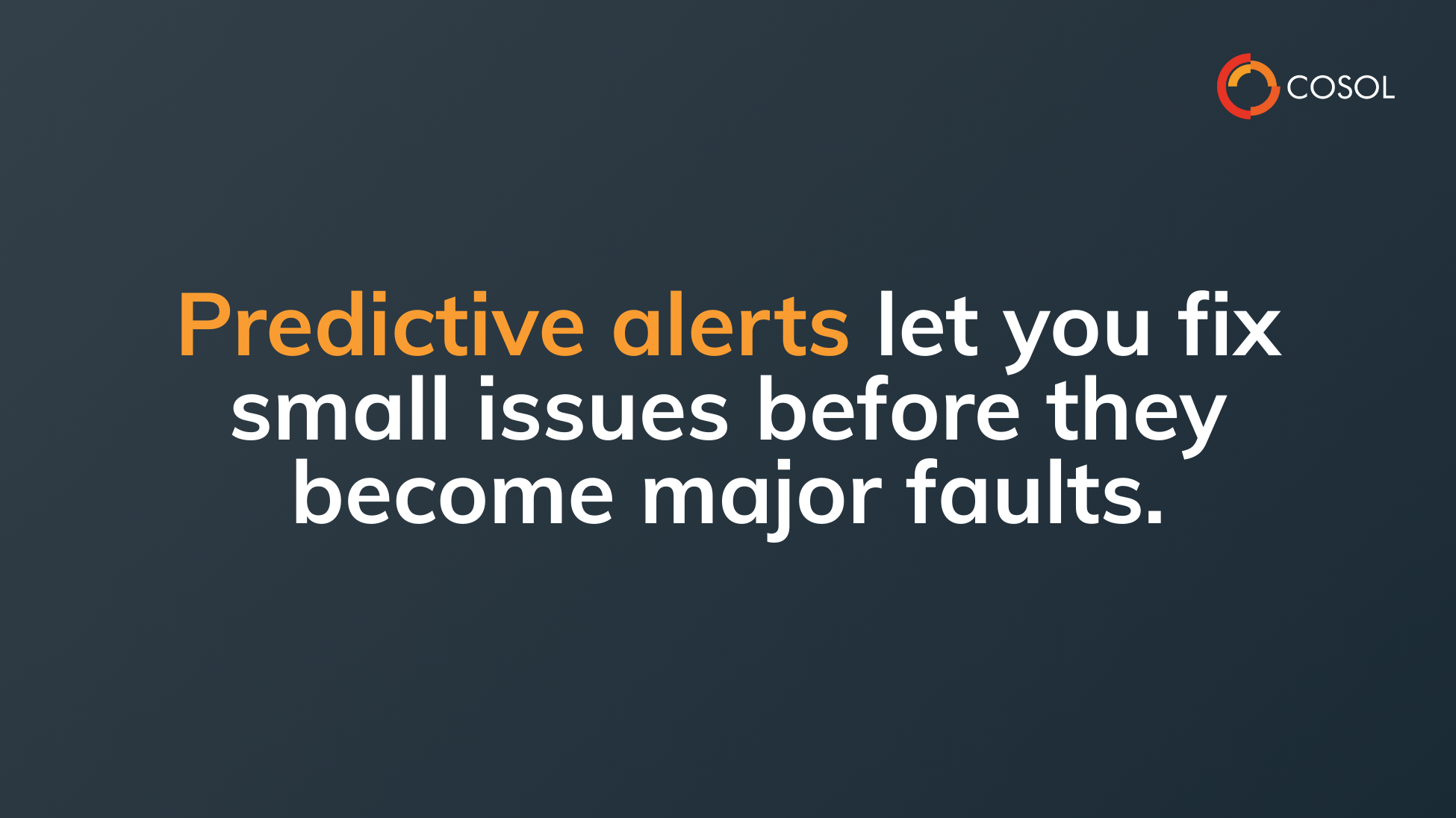
Building more resilient operations
Avoiding failure is important, but building resilience is what keeps services running. When teams can act early, plan ahead and trust their systems, performance improves.
When you empower asset managers with real-time insights, you’re not just avoiding downtime. You’re building trust in your infrastructure.
AI contributes to that by giving organisations:
- Greater confidence in asset condition
- Improved planning accuracy
- Early warnings before failure
- More efficient use of time and resources
These improvements also reduce stress on teams, improve communication, and lead to better decisions at every level.
Moving from reactive to ready
Transportation companies face complex, high-stakes decisions every day. But, I truly believe that with the right data, systems, and strategy, it's possible to move from firefighting to foresight.
Whether you're overseeing a regional fleet or managing a national logistics network, the key is integration. What I mean by this is bringing together operations, maintenance, compliance, and customer service into a single, connected view.
Because in this industry, keeping wheels turning (excuse the pun) isn't just about uptime. It’s about delivering on every promise, every time.
Using technology and data to make tangible business impact has been a focus of mine for decades. And I'm always happy to chat about it - let's connect.
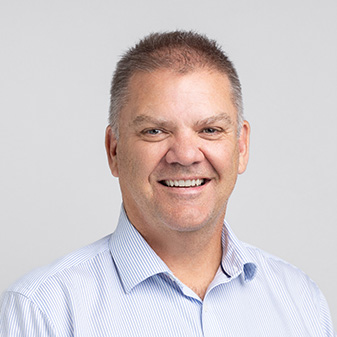
About Craig Lefoe
COSOL are IBM Gold Partners and IBM Maximo specialists with over 15 years experience helping asset intensive organisations implement and upgrade their EAM systems as part of their asset information ecosystem.
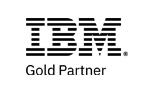