At a glance
-
Transportation businesses face growing complexity in balancing assets, schedules, safety, and customer expectations.
-
Maximo helps streamline operations through integrated data and real-time insights.
-
Predictive maintenance and smart routing reduce downtime and boost customer service.
-
Strong data-driven strategies enable transportation companies to stay competitive and compliant.
In transportation businesses, two of the most mission-critical roles - operations and maintenance leaders - often work side by side. While operations teams are under relentless pressure to deliver on-time performance, manage driver availability, and optimize fuel costs, maintenance teams are equally burdened with aging fleets, spare parts shortages, reactive work orders, and compliance documentation. Each function is doing its best to work seamlessly with the other - but achieving that is a challenge.
Misalignment can lead to delays, downtime, cost overruns, and frustrated stakeholders. On the other hand, lining them up brings significant advantages. When operations schedules match maintenance needs and prioritize preventative care, vehicles are confidently assigned without the risk of breakdowns or unnecessary idle time.
Current transportation industry trends include the introduction of smart, integrated enterprise asset management (EAM) technology to close the gap. By connecting data, workflows, and decision-making between operations and maintenance, modern EAM platforms enable transportation companies to move from firefighting to foresight. The prize is significant. EAM has the power to deliver:
- Improved asset availability
- Extended asset life
- Lower costs
- Improved customer experience.
In short, EAM can be the backbone of operational excellence in transport, if implemented with the right strategy.
Here’s why.
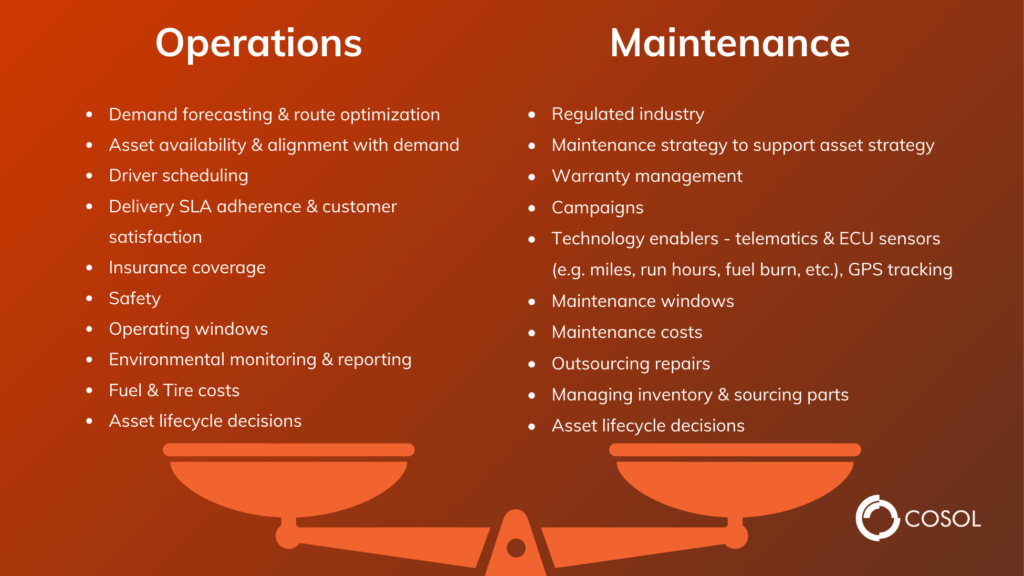
An Operations Perspective: Maximizing Transport Efficiency and Customer Service
In the high-pressure world of transportation, operations teams walk a daily tightrope - balancing the variables of freight demand, fleet availability, driver compliance, customer service expectations, and cost competitiveness. One misstep, whether a delayed delivery, a sidelined vehicle, or a missed permit renewal, can create a ripple effect across the business. The truth is, even the most seasoned operations leaders are often hindered - not by strategy but limited visibility.
This is where transport asset management platforms can change things.
Turning Data into Decisions
Whether forecasting the impact of a new customer contract, or adjusting for seasonal surges or weather (a sudden snowfall can bring chaos), transportation planners need instant access to consolidated asset and workforce data. COSOL’s EAM solutions unify maintenance and operational datasets into a single, real-time view - and that gives our customers intelligence to:
- Identify asset gaps early and adjust procurement pipelines based on actual lifecycle forecasts
- Map driver qualifications (including HAZMAT and oversized load certifications) to jobs, avoiding compliance violations
- Forecast cost implications of expanding or reducing the fleet - balancing fuel, tire, insurance, and servicing overheads.
Without integrated EAM data, these decisions often amount to spreadsheet-based assumptions and guesswork. But with it, they become informed, agile responses to market demand and massive operational efficiency drivers.
Customers Depend on Your Operational Agility
Now let’s add customer service in transportation into the mix. Today’s transportation customers demand more than basic services - they expect accuracy, speed, and full transparency, which you can give them via:
- Predictive ETAs via telematics integration
- Automated delay alerts and rerouting workflows
- Real-time compliance tracking to prevent disruption to services due to expired licenses or vehicle certifications.
These capabilities allow transport companies not just to fulfill contracts, but to actively protect and grow their customer satisfaction scores.
Optimization is the New Differentiator
The reality is, with rising operational costs and tightening margins, optimization is no longer optional - it’s strategic. EAM platforms like IBM Maximo Application Suite, configured to organisations’ unique needs by COSOL, can ingest telemetry, GPS, and fuel sensor data to optimize operations, improve asset performance, and boost technician productivity, reducing downtime and extending equipment lifespan.

Now let’s look at things from a maintenance standpoint.
A Maintenance Perspective: Keeping the Wheels Turning in Transportation
Transportation fleets depend heavily on complex equipment, which endures grueling mileages while facing strict inspection requirements. Fleet managers often find themselves juggling the intricacies of maintenance, balancing the need for maximum asset utilization with the capacity for repairs and parts availability.
Downtime in fleet operations can quickly cascade into poor customer service, contractual violations, and significant revenue impacts. Achieving mastery in fleet asset management means harnessing integrated data for planning, prediction, and efficient mobilization of both internal teams and external repairs, ensuring that off-road incidents are minimized.
Telematics technology in fleet maintenance software has revolutionized asset maintenance by capturing component faults as soon as electronic control units (ECUs) trigger threshold alarms. This increased visibility allows fleet managers to assess emerging defects flagged by fault code analytics, comparing them to scheduled preventive maintenance activities. By monitoring detailed usage metrics - such as fuel consumption, idle time, and operating hours - fleet managers can fine-tune the frequency and scope of campaign maintenance initiatives, ensuring that they address the most critical issues first.
Managing Maintenance Costs
When drafting maintenance budgets, it’s important to revisit replacement strategies to align with modern duty cycles, which can prevent premature failures. Analyzing the cost-effectiveness of outsourcing major foundational work versus insourcing routine maintenance activities can also provide valuable insights for more accurate resourcing plans. Advanced asset management software can sequence upcoming maintenance needs and balance labor allocations across different geographic locations, while factoring in things like required certifications, available bay space, and emerging backlogs.
Behind the scenes, efficient parts sourcing becomes a critical task, requiring fleet managers to sharpen supplier agreements and set minimum stock levels based on projected repair needs and expected delivery lead times. Meanwhile, warranty recovery opportunities can help offset maintenance costs - provided claims are submitted promptly, with all necessary substantiating evidence. This is where system integration plays a vital role, ensuring information flows smoothly to meet the deadlines for filing claims within the warranty period.
Predictive Maintenance: Transportation
In transportation, maintenance intricately ties with both safety mandates and customer delivery expectations.
In its operations and maintenance procedures guide, the Department of Transportation’s Federal Transit Administration points out that, “operations and maintenance procedures can result in hundreds of individual data points, advising transportation organizations to ask themselves, “What information do your workers need to carry out their SMS (safety management system) responsibilities?”, and, “How do you give them this information?”
EAM software’s ability to monitor, analyze, and predict potential issues through advanced technologies like predictive analytics, IoT sensors, and seamless system integrations gives fleet managers the visibility they need to identify problems early. This approach empowers decision-makers to act swiftly, keeping assets rolling and ensuring both operational efficiency and customer satisfaction.
In Conclusion
The integration of EAM solutions supports fleet management best practices - bridging the gap between operations and maintenance, providing transportation companies with the tools to make informed, proactive decisions. By unifying data, streamlining processes, and enabling predictive maintenance, EAM not only enhances fleet reliability and customer satisfaction but also drives significant cost savings and operational efficiency.
By uniting operational strategy with real-time asset intelligence, EAM becomes more than a back-office tool - it becomes the engine of competitive advantage.
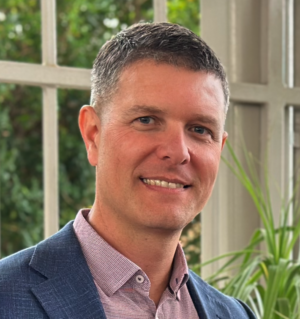
About David Lestani
Ready to see how EAM solutions streamline your transportation operations?
Contact us today to start the conversation and explore solutions tailored to your organization.
COSOL are IBM Gold Partners and IBM Maximo specialists with over 15 years experience helping asset intensive organizations implement and upgrade their EAM systems as part of their asset information ecosystem.
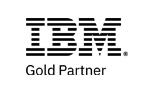