At a glance:
- AssetOn, a COSOL company (acquired in 2023) audited SAP master data for Glencore Coal, identified gaps and developed a plan to prioritise and fix these issues across 26 sites.
- They utilised software tools to validate data against best practices, creating SAP load files for updates, and ensuring consistency in maintenance tasks, plans, and BOMs.
- The outcome included more efficient planning, reduced administrative costs, and accurate maintenance budgets due to improved data quality.
Background
Glencore Coal Australia deployed SAP as their ERP and asset management system in 2016. Glencore Coal sites have been adding Maintenance Tasks, Maintenance Plans/Items & Bill of Materials on a site-by-site basis. While some good information was added to SAP, lack of a consistent approach led to the following issues:
- Not all parts had been catalogued leading to some parts being ordered outside of the system (direct purchase) incurring additional administration cost for each order.
- Maintenance budgets could not be prepared entirely from SAP data. The manual intervention takes time and the budget is not linked to the maintenance plan.
- Ad-hoc BOMs were needed for jobs were no BOM existed. This compromised quality and took additional planning time.
Project
AssetOn; a COSOL company, was engaged to perform an audit and support the data review and update. AssetOn handled the complete project from data audit to the creation of SAP load files to add/extend materials and update the parts catalogue. The project steps were:
- Audit SAP asset master data across 26 sites for Glencore Coal Australia
- Identify gaps in the data and prepare a report
- Build a plan to prioritise and fix issues identified in the audit
- Develop new data to fill the gaps in tasks, plans and BOMs
- Ensure site-validated BOMs in place for all major maintenance tasks and services
- Use any good work created by Glencore to date where possible
- If new data is created for one site/equipment, leverage this information for other sites that have similar equipment
- Catalogue parts added to BOMs (Extend parts to site if they exist in the master Catalogue or create new catalogue items)
- Created SAP load files to update the system with validated data
Approach
AssetOn has developed software tools and processes used by our master data team to efficiently audit, review and validate client Master Data against best practice. Clients can then make decisions about which data can be kept and what needs to be review. The tools guide clients by highlighting issues and making suggestions about action to take to improve the data quality. Once clients have validated the data, SAP load sheets are developed to update the master data.
The main parts of the process are:
- AssetOn provided a list of strategies for each asset to compare client task coverage on a site and equipment basis against best practice – Glencore could choose to add additional tasks from the list.
- An algorithm was used to identify variations at the part number level between client BOMs and AssetOn developed BOMs. Glencore then made decisions about what parts should be used. The algorithm also identified superseded and duplicate parts.
- The Algorithm compared the BOM data to Glencore’s master catalogue and identified parts as Catalogued, not catalogued or needing to be extended.
- The completed master data was sent to Glencore for final review. The algorithm highlighted errors for easy review by Glencore.
- To complete the project, AssetOn built the validated master data into SAP load sheets.
Outcome
The following outcomes were achieved for the project:
- Consistent execution strategy across multiple sites.
- Validated BOMs ensure the right parts are ordered for the job.
- More complete Task and BOM coverage increased the planners’ efficiency
- Catalogued parts reduce the administration costs order parts
- More accurate maintenance budgets can be created from the better quality / more complete master data reducing the risk of cost overruns.
About COSOL
Established in 2000, COSOL is now a leading global provider of asset management solutions that span the people, process, systems, and data elements of asset management. Since 2020, we have worked to expand the capabilities, services and solutions that we offer our customers worldwide. In 2020, we acquired North American company AddOns Inc., followed by Australia-based businesses Clarita Solutions in 2021 and Work Management Solutions (WMS) in 2022. The acquisition of AssetOn further builds on our goal to expand our footprint and capability by bringing expertise in asset maintenance software and services to COSOL across the East Coast of Australia. Learn more about Our History.
About AssetOn Group
In 2016, AssetOn was established in Australia to satisfy the demand for high-quality maintenance and asset management professionals within asset heavy industries. Since then, AssetOn has become the leading Australian provider of asset management skills, experience, and technology solutions and offer an expanded range of services to address asset management and maintenance inefficiencies. Learn more about AssetOn.
Mastering SAP 2024
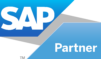