This is the third article in our series on optimising MRO inventory, and follows on from our our insights 'Decarbonise your operations with inventory optimisation', and 'Keys to MRO inventory optimisation success.
At a glance:
- Optimised Maintenance, Repair and Operations (MRO) inventory can reduce inventory costs by up to 40 per cent*, with immediate benefits and payback within the first year.
- Inventory optimisation activities must take into account an organisation’s unique operating methods and strategic objectives.
- The challenges of managing MRO inventory can be varied, including extensive input variables and collaboration issues across functional areas.
- COSOL’s Inventory Optimisation Opportunity Assessment will investigate your organisation’s current state, identify areas of opportunity then provide observations and recommendations to help your organisation realise tangible benefits.
Achieving inventory optimisation starts with your inventory strategy. This strategy is then technology-enabled to harness the power of your organisations data and policies through statistical analyses, prescriptive analytics and optimisation algorithms. The result is improved margins, increased service levels, and minimised unplanned downtime due to parts.
An Inventory Optimisation Opportunity Assessment by COSOL can identify inefficiencies and opportunities to leverage strengths in your organisation’s inventory management operations and strategies. Through the assessment process, your organisation will:
- begin to understand the level of opportunity and cost savings that inventory optimisation can achieve;
- what technology, process and data solutions are required to maximise that opportunity; and
- how to approach your inventory optimisation project.
Organisations can reduce inventory costs by as much as 40 per cent when they optimise MRO specific inventory - benefits can be realised within one month and payback on implementation of a specific MRO inventory optimisation solution can be achieved within 12 months.*
Inventory optimisation challenges and opportunities
With MRO inventory values often reaching from fifty to hundreds of million dollars and growing year on year, organisations face many challenges managing their MRO inventory, including understanding the true value of their inventory and identifying the potential cost savings that can be achieved through efficient inventory management.
Other challenges asset intensive organisation face include:
- large numbers of unique MRO parts, tools and other consumables;
- extensive input variables, such as lead time, criticality, location of parts, and supplier type;
- demand and supply variations caused by process changes, production changes, acquisitions, decommissions, and changes to ERP/EAM software and processes;
- the need to accurately factor in critical costs, such as procurement, downtime and holding; and
- collaboration issues across functional areas including supply chain, materials management, maintenance, reliability and operations.
Examples of industry specific challenges include:
- Energy & Utilities: storm season stock; network expansions; asset lifecycle stage (new, in-service & aging, sunset);
- Mining: lifecycle-stage of each operation (greenfields, growth, consolidation or decline); economic cycle and commodity pricing; fleet expansion or retirement; asset lifecycle stage;
- Oil & Gas: commodity pricing uncertainty & volatility; asset lifecycle stage; relocation of assets; seasonal variation; storage capacity constraints at remote operations
Understanding the unique challenges each organisation faces is essential in evaluating potential benefits and what inventory optimisation solution is right to meet its needs and objectives. Organisations that engage in a systematic and tailored approach to implementing an inventory optimisation solution can benefit from accurate and consistent results in their inventory management.
Opportunities that optimising MRO inventory provides include:
- Inventory managers can overcome visibility and data sharing challenges by gaining a real-time view of their organisation’s supply chain and stock levels;
- Operations and maintenance teams can expect to see a reduction in unplanned downtime relating to parts, and better service levels; and
- Finance teams can unlock valuable working capital.
While the cost of not include:
- Bloated inventory levels
- Increased storage and logistical costs
- Increased carbon footprint
- Increased equipment downtime
- Capital tied up including in obsolete parts
- Increased headcount
Why an Inventory Optimisation Opportunity Assessment is the critical first step
When inventory levels are ‘right-sized’ with inventory optimisation, asset managers can make informed decisions about their inventories. That way they can ensure they carry ‘never too much, and always enough’ stock, parts and other consumables. Undertaking a COSOL Inventory Optimisation Opportunity Assessment is a critical first step as it enables organisations to uncover hidden efficiencies and missed opportunities in their operations, and develop strategies to find the optimised balance between holding an excess of inventory and not having enough.
It helps them re-examine their policies especially if the opportunity assessment determines that there are discrepancies in their organisations performance compared to their industry averages – such as for the material criticality rankings across their industry sector, or by comparing their safety stock holding levels relative to similar organisations.
COSOL’s Inventory Optimisation Opportunity Assessment is undertaken in 3 stages:
1. Benchmark Assessment
We begin with a benchmark assessment to determine the value to your organisation optimising it's MRO inventory based on peer organisation benchmarks. This benchmarking includes looking at MRO inventory values and segmentation to establish what ‘best-in-class’ practices have been adopted by industry leaders and what ‘average’ inventory optimisation looks like for your business. Your current inventory levels, procurement strategies and supplier relationships are compared to these benchmarks and assessed to measure how they align with industry standards and trends.
The assessment will equip your organisation to clearly understand your key benefits of inventory optimisation and associated improvement benchmark ranges and optimal targets.
2. Stakeholder Workshops
Once the benchmarking assessment is complete, COSOL conducts workshops with key stakeholders in your organisation as part of a current-state review of inventory strategy and practices. Alongside the Benchmark Assessment Report, this review helps to qualify the inventory optimisation opportunities available to your organisation.
3. Deep analysis of inventory data
This stage is about value validation of the opportunity by diving deeper into a sample of your own data to provide a more accurate understanding of the opportunity and the pathway to realise these benefits.
Once all three stages are complete, COSOL provides your organisation with a comprehensive Opportunity Assessment Report that clearly outlines what opportunities your organisation can unlock – and what specific actions should be taken to improve MRO inventory performance.
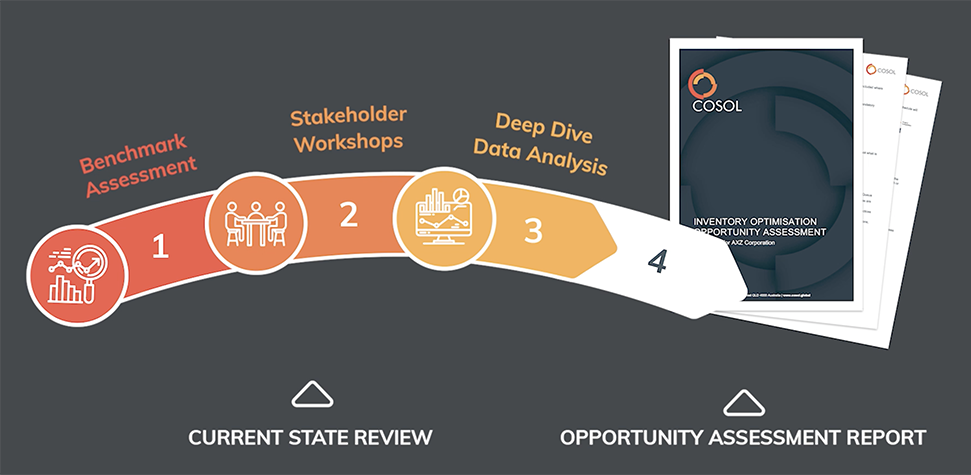
Get started with an Inventory Optimisation Opportunity Assessment from COSOL
COSOL can get your organisation started on your journey to optimised MRO inventory. Our Opportunity Assessment will determine what value can be gained from optimisation of your MRO inventory and what process, technologies and solutions are needed to maximise the benefits.