The advantages of embracing Building Information Modelling (BIM) in design and construction (D&C) have been well and truly proven. Large infrastructure projects now mandate that BIM be used to centralise data, facilitate communication and promote efficiencies across the early stages of the lifecycle of built assets and infrastructure. But out of an operational service life that could span tens, if not hundreds of years, the adoption of BIM seems to fizzle out once construction crews pack up and the asset is handed over to operations and maintenance (O&M).
Although BIM isn’t exactly bleeding edge technology, the buzz is steadily growing as advancing animation, virtual/augmented reality and gamification techniques apply BIM data in creative and innovative ways. Ever-shrinking margins continually fuel the search for the means to increase efficiency, improve data accuracy, and reduce time-consuming and costly rework across large construction projects.
The hype around BIM as the answer to design and construction issues has certainly led to a general lack of awareness and understanding of its potential for asset operators and maintainers (and where there’s hype, there’s always jargon and buzzwords to make it sound complex and confusing!), but there are also a number of practical barriers standing in the way of wider BIM adoption across the entire asset lifecycle.
The problems with BIM beyond construction
The challenges in embracing BIM across D&C and O&M teams essentially boil down to contractual issues, understanding of digital engineering requirements to support O&M, the quality of models received and how they can be applied to support delivery teams.
Consider the BIM value chain across the asset lifecycle:
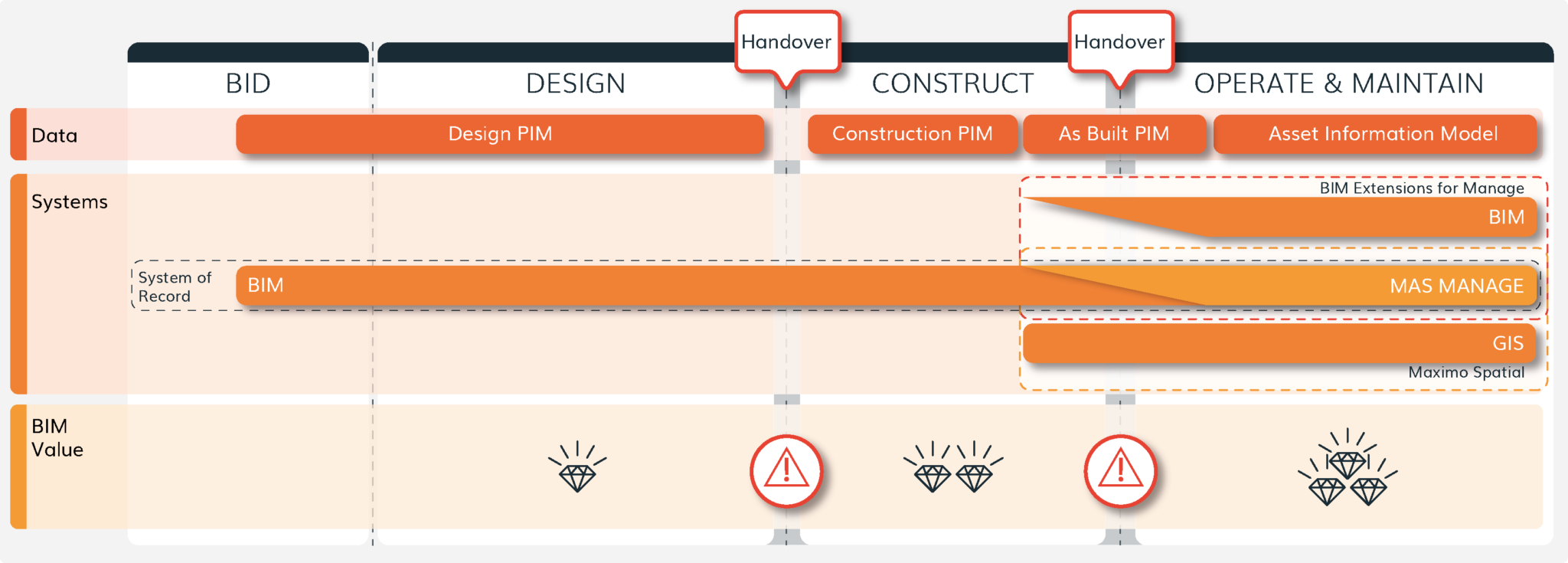
The Project Information Model (PIM) is established at the very beginning of the design process, long before O&M requirements and providers are even considered. It stands to reason then that the model is developed with D&C needs in mind. Although this serves the project well in the early stages, it can result in a PIM that is difficult (although not impossible, more on this later)Â to apply in support of asset operations, particularly if there has been poor handover between each phase of the asset lifecycle. As a result, the value for the asset owner (who invested in BIM from the outset) is diminished and the poor experience leaves little incentive for O&M teams to attempt further efforts.
Here are some of the common issues observed:
1. Contract Specifications & Deliverables
Initial design and construction contract documents don’t always specify BIM as a project completion deliverable, and when they do, the standards are not always specified. This leaves the way open for individual contractors to use their own tools and approach, defeating the goal of providing a coordinated handover to operations with streamlined data workflows and standardised data sets centred around a foundational model.
Without a coordinated approach:
- increased risk that the model will be lost during handover between stages.
- model does not meet the needs of operations and teams resort to manually crafting data from other sources
- timing to deliver as-built federated models (particularly where multiple versions and/or large files are involved) don’t meet the timeline for commissioning.
2. Understanding of O&M use cases from the outset
As one mining industry client discovered after engaging BIM consultants on a mine augmentation and expansion project, the digital engineers responsible for establishing the PIM often have limited knowledge of the operations and maintenance use cases. The project was completed and only when queried as to why it was not being utilised to support operations did the asset owner know that this was possible.
At COSOL, we address this issue by working together with digital engineering specialists DBM Vircon who are committed to fostering early conversations between O&M and D&C and replacing chaos and urgency with a managed foundational data set, a coordinated handover to operational teams and ongoing curation of these important digital artefacts.
3. Quality of Models received
Project Information Models (PIM) employed in design and construction stages are different to the Asset Information Model (AIM) needed to maintain the asset over time. When the model is simply passed over the fence on completion, they can rarely be integrated with enterprise asset management systems (EAMS) like IBM Maximo Application Suite (MAS) without considerable effort. The asset management team at a COSOL water utility client received the PIM on handover of a new sewage treatment plant, only to find it was completely unusable due to misalignment with their EAM.
A managed handover, however, will ensure that the model conditioning has been completed, which means that the information needed to make it useful for future phases of the project has been added. Some of the common issues include gaps in the primary keys, inconsistent geometries, different (or perhaps non-existent) naming conventions and a disconnect between model objects and EAM attributes.
4. Available Expertise
The Digital Engineering expertise required to generate and maintain BIM approaches are often only engaged during the early D&C stages. Once the asset is handed over to operations, the expertise moves on and BIM value begins its downward spiral…it’s not seen as being worth further investment in maintaining models that aren’t delivering value, but it’s the very lack of maintenance that fuels diminishing returns.
The asset operators breaking down barriers
Together with our Digital Engineering partners, DBM Vircon, COSOL are observing a changing appetite for BIM approaches in asset operations, with promising results. One of DBM Vircon’s oil and gas sector clients has realised savings in the order of $500M through improved operational and asset management processes that leverage the AIM.
Other examples currently in progress include:
- a metropolitan road and tunnel network O&M provider was keen to utilise BIM to inform creation of the asset information register, but digital handover was not a deliverable the construction consortium was contracted to supply. The fallback was a cumbersome and error prone process of building the asset register from spreadsheets. Efforts to reconstruct the model have since been made and a proof of concept to visualise planning and asset health has been completed using MAS. This has generated valuable insight on factors critical for successful BIM to IBM Maximo integration.
- DBM Vircon and COSOL are supporting the development of an extensive underground rail construction project in Queensland, Australia where BIM is mandated for all public construction projects over $50M. While construction is not due to be completed until late 2024, we are currently building a BIM to IBM Maximo integration solution that will streamline commissioning of the new infrastructure by converting the PIM into an AIM and then connecting it to the asset information register.
Automate creation of the asset register from BIM
Like many asset operators, you may find that you’ve inherited an As Built PIM along with a new asset, and have no idea what to do with it. Importing it into MAS Manage to inform the asset register and maintenance requirements is possible, but it’s likely to require technical expertise.
In order to make use of BIM in IBM MAS, it needs to be reconstructed from the native applications in which they were created (ie: the design software appropriate to each of the trades involved – electrical, water, fire and so forth) into a final federated model. This involves removing the finer detail that is not relevant to maintenance, for example, every nut & bolt or part needed for quantity surveying or material procurement.
Some of the core conditioning activities include:
- Feature objects grouped at a level that is appropriate for the asset being managed (we want an entire handrail, we do not want the top, middle & bottom rails and vertical joins as separate assets)
- EAM functional locations linked to their respective BIM feature geometries
- BIM objects, when basic federation methods are employed, are organised by trade in locations and spaces, while IBM MAS is built on locations, items and assets. Establishing a model navigation hierarchy that reflects where the assets are found provides alignment to EAM functional location hierarchies. The responsibility for the asset is then handed over from BIM to EAM.
- Removing attributes that do not add value to maintenance.
For example, in BIM an item may include attributes like scannable ID, room, measurements, serial number and construction status. In MAS, attributes like construction status are not relevant to maintaining the assets and others need to be mapped to the appropriate counterpart (Room to Location for example).